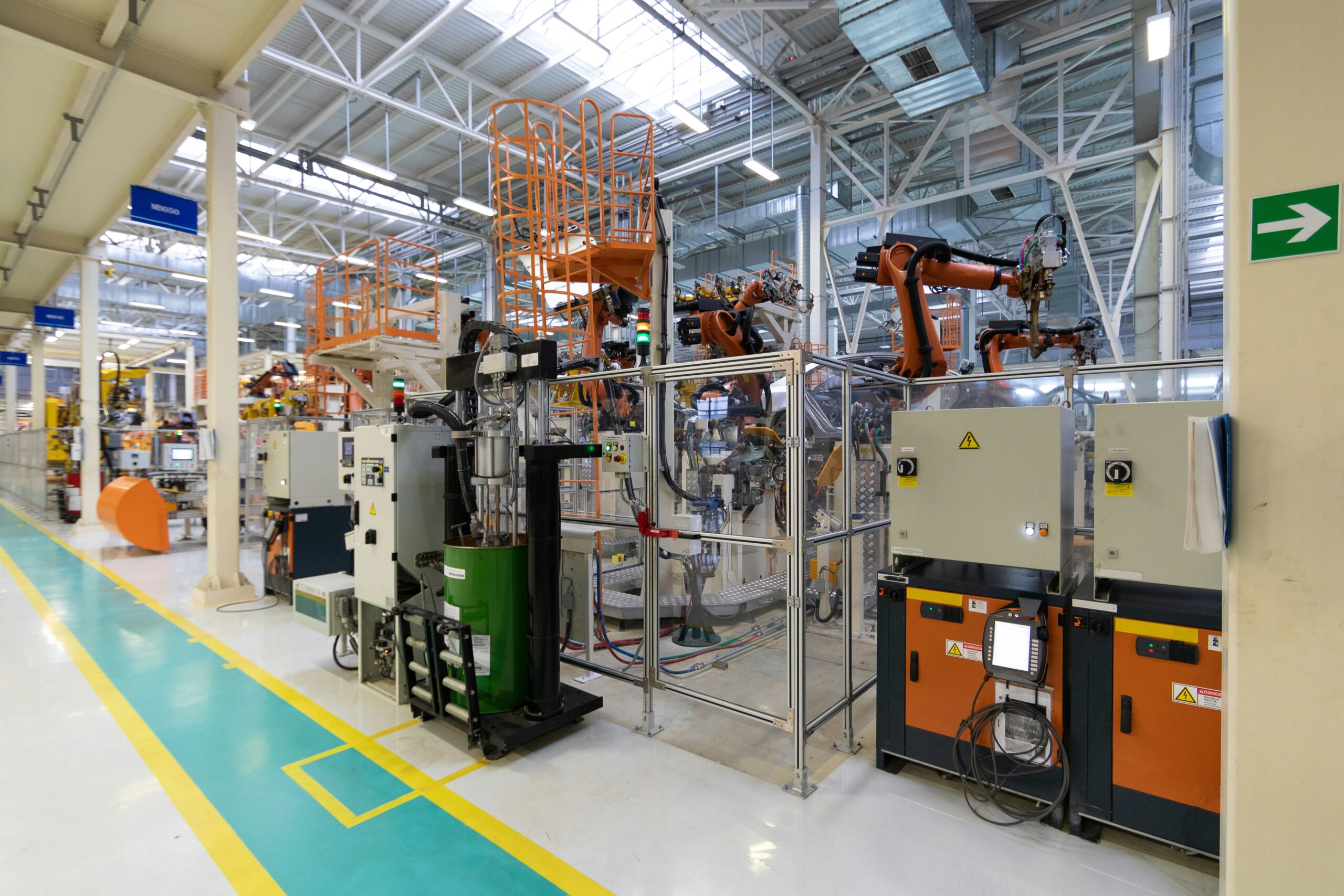
In today’s fast-paced business environment, manufacturers are constantly pressured to increase productivity while minimizing costs. Optimizing manufacturing operations is crucial to remaining competitive and meeting growing consumer demands. Streamlining processes, enhancing efficiency, and incorporating modern technologies can significantly impact output, ultimately improving profitability and long-term sustainability. This article delves into strategies manufacturers can adopt to maximize production.
Assess Your Current Operations
Before implementing any changes, a deep dive into your existing manufacturing processes is essential. Evaluating your current operations will allow you to identify areas that need improvement. Gather data on production speeds, downtime, waste, and employee performance. A comprehensive analysis of these factors can help pinpoint inefficiencies in your workflows, equipment, or labor management.
Once you’ve identified the bottlenecks in your system, you can focus on developing targeted solutions to resolve them. Whether that means upgrading outdated machinery, improving staff training, or redesigning the layout of your facility, understanding the root causes of inefficiency is the first step toward optimization. You can track progress and make real-time adjustments to improve productivity by continuously monitoring performance metrics.
Implement Lean Manufacturing Principles
Lean manufacturing is an approach focused on minimizing waste and maximizing value. Adopting lean principles can lead to significant improvements in efficiency and output. This includes streamlining production processes, eliminating unnecessary steps, and reducing overproduction. By focusing on what adds value and cutting out the rest, you can create more efficient workflows and reduce costs.
Continuous improvement is a key component of lean manufacturing, also known as Kaizen. This mindset encourages employees at all levels to contribute ideas for improving safer and more efficient processes. By involving your entire team in problem-solving, you create a culture of innovation that drives long-term success. Maintaining a clean and organized workspace (5S methodology) enhances safety and reduces the time spent searching for tools and materials.
Utilize Automation and Technology
Introducing automation and advanced technology is one of the most effective ways to optimize manufacturing operations. Robotics, artificial intelligence, and machine learning can help streamline repetitive tasks, reduce human error, and increase production rates. Whether it’s automated assembly lines or predictive maintenance software, technology can significantly boost your operational efficiency.
Investing in automation increases output and improves consistency and quality. Automated systems work around the clock without the fatigue or limitations humans face. Additionally, data gathered from these systems can provide valuable insights into performance and potential improvements. Integrating technology into your manufacturing processes allows you to create a more flexible, scalable operation that adapts quickly to market demands.
Focus on Employee Training and Engagement
Employees are the backbone of any manufacturing operation. To maximize output, it’s vital to ensure that your workforce is adequately trained and highly engaged. Skilled workers who understand the intricacies of your processes are better equipped to identify inefficiencies and contribute to process improvements. Regular training and upskilling programs will ensure your team is always prepared to adapt to new technologies and methodologies.
Engaged employees are also more motivated and productive. Encourage open communication and foster a positive work environment where employees feel empowered to share ideas. Recognizing and rewarding contributions to operational improvements can further motivate your team. By creating an environment that values continuous learning and improvement, you can unlock the full potential of your workforce.
Optimize Supply Chain Management
A well-managed supply chain is critical to maximizing manufacturing output. Delays or disruptions in the supply chain can halt production and lead to costly downtime. To optimize this aspect of your operations, focus on building strong relationships with your suppliers and establishing a reliable, just-in-time inventory system. This approach ensures that materials and components are available when needed, minimizing the risk of shortages.
Additionally, incorporating digital tools such as supply chain management software can help you track inventory levels, monitor order statuses, and predict demand fluctuations. Real-time visibility into your supply chain allows you to make more informed decisions and reduce the likelihood of stockouts or overstocking. A well-oiled supply chain supports smooth manufacturing operations, ensuring production runs efficiently and meets customer demand.
Enhance Quality Control Measures
Quality control is an essential component of optimizing manufacturing operations. At the same time, it might seem like an added expense, but ensuring consistent quality can save money in the long run by reducing defects, returns, and rework. Implementing strict quality standards at every stage of the production process will help identify issues early and prevent costly mistakes down the line.
Advanced inspection techniques, such as automated visual inspection systems, can help detect defects more precisely. Moreover, fostering a quality culture among employees ensures everyone is committed to maintaining high standards. Continually improving your quality control processes enhances customer satisfaction and strengthens your brand’s reputation, ultimately contributing to sustained business success.
Maintain Equipment and Machinery
Proper maintenance of equipment and machinery is crucial in maximizing manufacturing output. Well-maintained machines run more efficiently, reducing the likelihood of unplanned downtime and costly repairs. Establishing a preventive maintenance schedule helps identify potential issues before they become serious problems, keeping your production lines running smoothly.
Furthermore, implementing condition-based monitoring systems can provide real-time data on the health of your machinery. By using sensors and predictive analytics, you can schedule maintenance at the optimal time, preventing unnecessary shutdowns and extending the lifespan of your equipment. A well-maintained facility operates efficiently, reducing the risk of costly breakdowns and increasing overall output.
Foster a Culture of Continuous Improvement
Finally, creating a culture of continuous improvement within your organization is key to long-term success. Manufacturing optimization is not a one-time project but an ongoing effort to refine processes and adapt to changing conditions. Encourage employees at all levels to identify areas for improvement and provide them with the tools and resources to implement their ideas.
Regularly reviewing performance metrics and analyzing production data can help identify new opportunities for optimization. By fostering an environment of constant learning and innovation, you can ensure that your manufacturing operations remain competitive and efficient. This commitment to continuous improvement will help you maximize output, reduce costs, and drive sustainable growth for your business.